Benchmark Cleanroom White Paper
Introduction
This white paper explores the critical role and complexities of cleanroom services within chemical operations through:
- Cleanroom management
- Cleanroom services
- Importance and benefits of drip tube exchanges
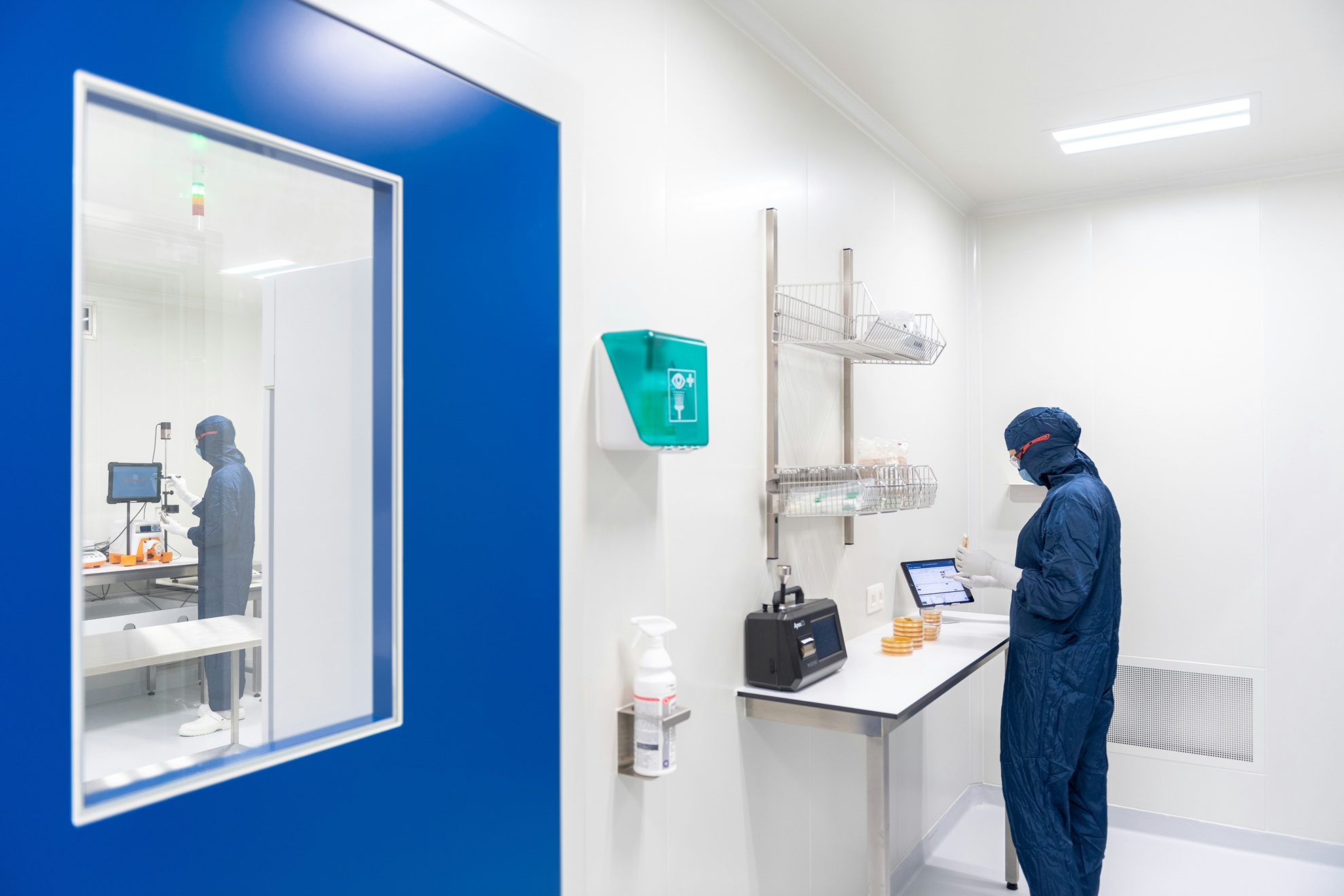
Cleanroom Management
Safety
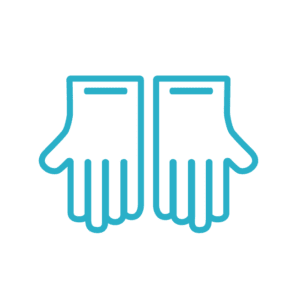
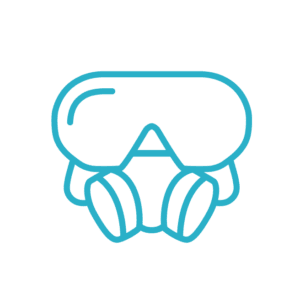
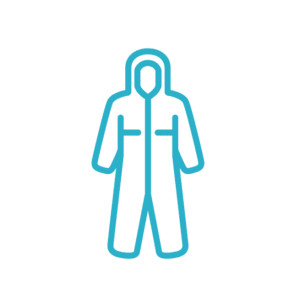
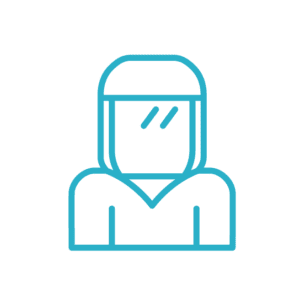
Training & Certification
Cleanroom employees undergo rigorous training and are required to become certified in many areas before beginning any work in a cleanroom environment. Employees are trained and re-certified yearly in cleanroom operations and procedures. In addition, cleanroom workers undergo health screenings yearly to determine that they are still able to safely carry out cleanroom procedures which are very physically demanding. Cleanroom workers must also re-certify with their respirators every year. They are certified to ensure they are still healthy enough to wear a respirator for extended periods, that their knowledge and utilization of the respirator is up to OSHA safety standards, and to check if the custom fit of their respirator needs any adjustments.
Cleanrooms are also certified yearly. This includes all the equipment in the cleanroom as well as the overall safety of the cleanroom operation. Tools and particle counters are calibrated and all data while work is being performed is stored to ensure no performed work was outside the allowable parameters. Specific work instructions are used to ensure that all cleanrooms across Rinchem meet the same safety standards and maintain their ISO Class 5 certification.
- All Equipment Calibration
- Safety Standards
- ISO Class 5 Standards
- Cleanroom Safety and Operations
- Health Screenings
- Respirator Knowledge
- Respirator Fit
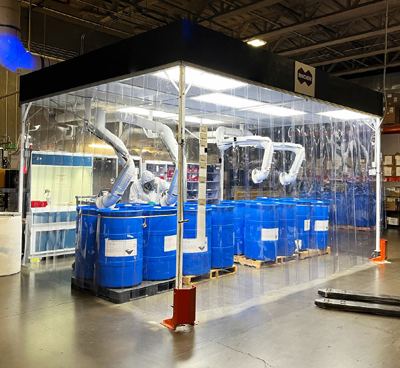
Processes
Maintaining a rigorous set of protocols ensures safe and standardized work across all Rinchem cleanrooms. Protocols can also be tailored to customer needs. Not all customers or chemicals will have the exact same set of requirements. Extra steps can be added to specific product or customer protocols that specify torque specifications or O-ring variation. Rinchem also sets a threshold for the maximum number of cleanroom operations that can be completed per day to ensure that employees are not overrun and are able to maintain the high level of product integrity and not sacrifice quality.
The capability to customize how the work if performed, while ensuring that it is performed in exactly the correct way every time is crucial to the integrity of chemicals for both chemical manufacturers and product users.
+
CLEANROOM SAFETY
+
EMPLOYEE CERTIFICATION
+
CLEANROOM CERTIFICATION
+
STANDARDIZED PROCESSES
=
Cracked Bung Opening
Foreign Material in Tube
Missing External O-Ring
Crooked Cap Installed
Damaged O-Ring
Cut on External O-Ring
Unseated External O-Ring
Incorrect Cap Installed
Fracture in Tube Threads
Foreign Material in Well
Foreign Material in Container
Cleanroom Services
Dip Tube Exchange
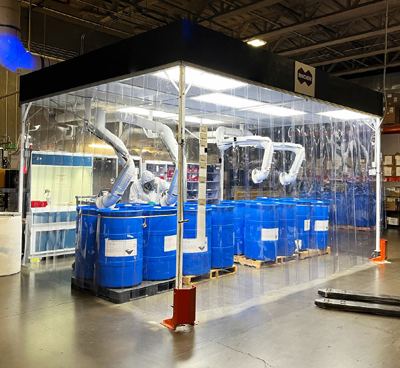